Whether it's people, machines, or materials—effective resource management directly impacts productivity, cost-efficiency, and customer satisfaction. But without transparency, it’s hard to spot bottlenecks early or make full use of unused capacity.
Efficient capacity planning helps you overcome these challenges. In this article, you’ll learn how to improve your capacity planning and why accurate capacity measurement leads to better business decisions.
What Is Capacity Planning and Why Is It Important?
Capacity planning ensures that your company has the right resources available at the right time. It covers areas such as:
- • People - Who is working on what, and when?
- • Equipment - Are machines running at full capacity, or sitting idle?
- • Materials - Are enough raw materials or goods in stock?
Without structured planning, you risk:
- • Bottlenecks that delay production
- • Excess capacity that drives up costs
- • Poor resource utilization that lowers productivity
Companies that improve their capacity planning can respond faster to changes, reduce costs, and gain a competitive edge.
Capacity Measurement: The First Step Toward Optimization
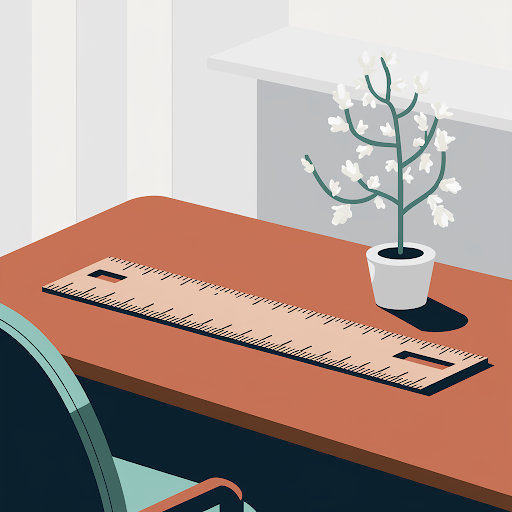
Before you can improve your capacity planning, you need a clear picture of where you stand today. Precise capacity measurement helps identify bottlenecks and uncover unused potential. Only by understanding how your resources are truly being used can you make smarter planning decisions.
Key Metrics to Track:
-
1. Utilization Rate
How much are your teams, machines, or storage spaces being used? Where are resources over- or under-utilized? -
2. Average Processing Times
How long does it take to complete tasks, projects, or services? This reveals where you can streamline workflows. -
3. Downtime
Where are you losing valuable capacity? Are there delays between tasks or idle resources at specific times?
Methods for Measuring Capacity
-
1. Total Effective Equipment Performance (TEEP)
Measures how effectively your equipment is used compared to its maximum capacity. Helps detect unused potential and avoid production slowdowns. -
2. Employee Productivity
Tracks how many productive hours your team delivers daily. Useful for identifying ways to optimize working hours. -
3. Planned vs. Actual Project Times
Comparing estimated and real workloads shows whether your planning is realistic or if inefficiencies exist.
Why Accurate Measurement Matters?
Without in-depth analysis, bottlenecks and idle resources often go unnoticed. Companies relying on estimates or outdated Excel sheets waste valuable resources and incur unnecessary costs. Data-driven capacity measurement uncovers optimization potential—laying the foundation for smarter resource use.
Strategies to Improve Your Capacity Planning
Efficient capacity planning goes beyond reacting to bottlenecks—it involves proactive thinking, flexible resource allocation, and smart technology use. Here are three proven strategies to take your planning to the next level:
-
1. Plan Ahead, Don’t Just React
Many companies adjust their capacities only once bottlenecks become obvious—but by then, it’s too late. Shortages cause delays, overworked teams, and missed opportunities.Tip: Analyze historical data to uncover trends or seasonal patterns. Are there recurring peaks in demand? Use these insights to plan ahead and avoid overload.
Example: A manufacturing company notices that demand for certain components rises by 30% in Q2 every year. By pre-planning additional capacity, they prevent delays and fulfill orders on time.
-
2. Dynamic Resource Allocation for Greater Flexibility
Rigid capacity plans may work on paper but often fail in practice. Unexpected events—like urgent client requests, sick leave, or supply chain issues—can quickly throw fixed plans off course.Advantage: Dynamic capacity planning allows for flexible reallocation of resources, making it easier to adapt to changes and avoid bottlenecks.
Example: A construction firm uses automated capacity planning to coordinate material deliveries across sites. The software analyzes project progress and predicts when specific materials will be needed, avoiding costly delays and stockouts.
-
3. Automate Your Capacity Planning
Manual planning in Excel or outdated tools is not only time-consuming—it’s also error-prone. Modern capacity planning software allows for real-time adjustments and full visibility, helping you make smarter, faster decisions.- • Less Time Spent Planning – Smart algorithms handle resource assignments for you.
- • Optimized Resource Use – The system flags bottlenecks early and suggests solutions.
- • Faster Adaptation – Plans update automatically to reflect changing needs—no manual fixes required.
Benefits of Automated Capacity Planning:
Example: A logistics company uses automated planning to match available storage and staff to incoming orders in real time. As a result, they manage demand spikes more efficiently and reduce warehouse costs.
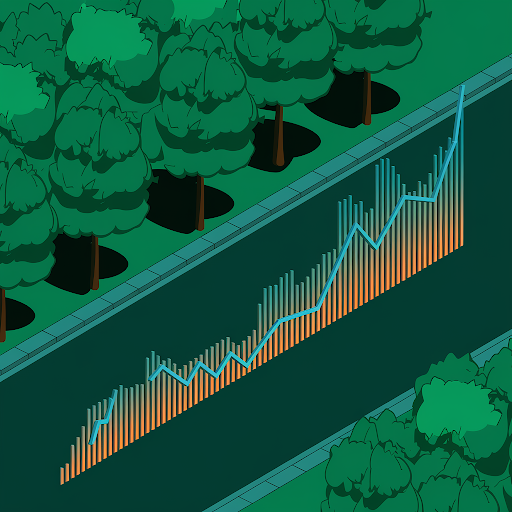
Smarter Capacity Planning Means More Efficiency and Growth
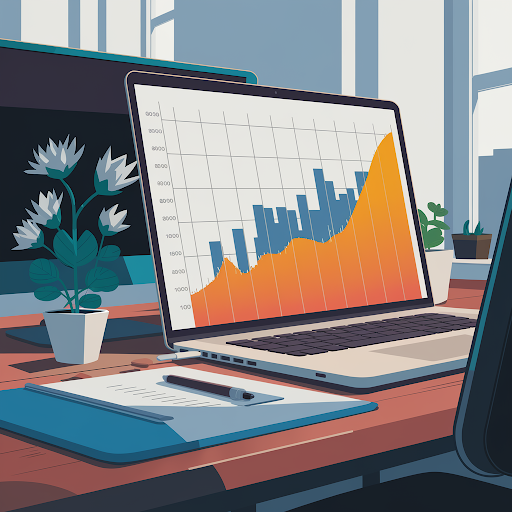
Companies that stick to manual or rigid planning methods risk delays, inefficiencies, and higher costs. By switching to a proactive strategy, flexible resource management, and automated tools, you can streamline your operations and stay ahead of the competition.
Early investments in planning efficiency pay off—with less stress, fewer errors, and more sustainable growth.
Why Modern Capacity Planning Is a Must?
By improving your capacity planning, you gain key advantages:
- • More Efficiency through optimized resource use.
- • Better Forecasting thanks to accurate measurement.
- • Greater Flexibility through proactive and automated processes.
Whether you're in manufacturing, services, or logistics—professional capacity planning is essential. Those who optimize it save costs, boost productivity, and build long-term success.
Want to improve your capacity planning? Discover how our capacity planning software, CapaPlanner, can help your business thrive.