Effective capacity planning is the foundation of efficient production with minimal downtime. With the right approach and the use of Total Effective Equipment Performance (TEEP), you can optimize machine usage and avoid production bottlenecks.
In this article, you'll discover why precise resource management is essential in manufacturing, how to calculate your actual equipment utilization with TEEP, and which steps can elevate your production processes to the next level.
Why Capacity Planning in Production Matters?
Smart production planning is the backbone of a profitable operation. Without it, companies face uneven workloads, unnecessary downtime, or costly overcapacity.
Proper planning enables:
- • Shorter lead times and higher productivity
- • Reduced machine downtime and maintenance costs
- • Better coordination of personnel and material use
- • Improved customer satisfaction through reliable delivery times
Especially in volatile markets with fluctuating demand, accurate planning helps you stay agile and profitable.
Common Challenges in Production Resource Management
Despite many optimization tools, manufacturers still face persistent challenges:
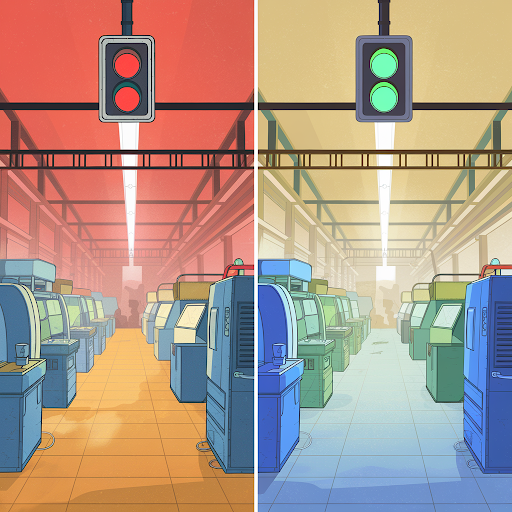
-
• Lack of transparency:
Without real-time data on machine capacity, material inventory, or workforce availability, proactive planning becomes nearly impossible.
-
• Underutilized equipment:
Machines often don’t run at full efficiency. Poor shift scheduling and unplanned stops cost valuable production hours.
-
• Fluctuating demand:
Unpredictable order volumes make it hard to allocate resources correctly — leading to either overcapacity or bottlenecks.
-
• Poor coordination between departments:
If sales, production, and procurement don’t align, delays and unnecessary inventory costs follow.
How TEEP Reveals the Real Efficiency of Your Equipment?
A key metric in production resource management is Total Effective Equipment Performance (TEEP). It shows how effectively your equipment is being used compared to its theoretical full-time capacity — helping uncover hidden optimization potential.
How TEEP is Calculated?
TEEP is made up of two major components:
-
• Overall Equipment Effectiveness (OEE)
Measures how efficiently a machine runs during operational hours (includes availability, performance, and quality).
-
• Utilization Rate
Reflects how much of the total available time (24/7) is used for production.
Formula:
FTEEP = OEE × Utilization Rate
Example:
A machine could theoretically run 24/7 but is only used 60% of the time. Its OEE is 70%.
TEEP = 70% × 60% = 42%
That means the machine is operating at only 42% of its full potential — a clear signal for improvement.
Why TEEP Matters?
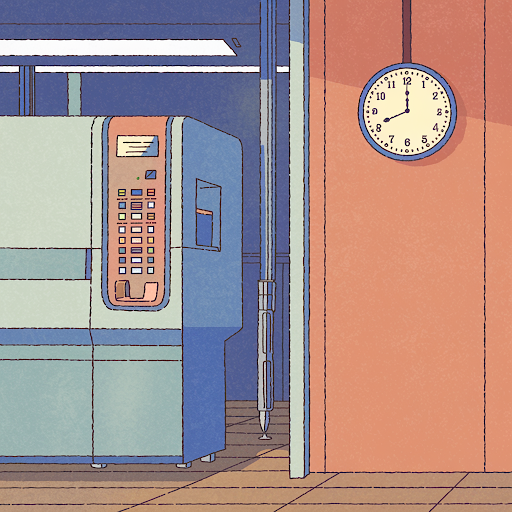
TEEP is a powerful indicator of your true production efficiency. It reveals how well your equipment is utilized — and where untapped capacity lies. With TEEP insights, companies can estimate how much more output is possible with smarter planning and streamlined processes.
- A high TEEP score indicates effective, near-continuous utilization.
- A low TEEP score reveals idle times or avoidable downtimes.
This makes TEEP an essential tool for identifying bottlenecks before they disrupt production — and for unlocking hidden productivity gains.
Bottom line: TEEP is your key to maximizing production capacity. Reducing downtime and improving machine usage not only boosts productivity but also gives you a competitive edge.
What’s a Good TEEP Score?
It depends on your industry and production setup, but here are general benchmarks:
- 100% TEEP: Perfect, round-the-clock usage - theoretically ideal, practically unattainable
- 80–90%: Excellent - optimal machine time utilization
- 60–80%: - room for improvement but generally acceptable
- Below 60%: - signals idle time, inefficiencies, or process issues
Pro Tip:
The best results come when high OEE is combined with high utilization. So optimize both machine performance and total available runtime.
5 Steps to Improve Your Production Capacity Planning
To avoid bottlenecks, cut costs, and boost productivity, companies must align machine time, staff availability, and material flow. Here’s how to do it:
-
1. Know Your Current Production Capacity
Create a detailed overview of your machines, staffing, and materials. Use digital tools with real-time data to stay on top of bottlenecks and respond quickly.
-
2. Use TEEP and OEE as Decision-Making Tools
Regularly track these KPIs to spot weaknesses and plan targeted improvements. Preventive maintenance reduces unplanned downtime, and optimized shift planning helps minimize idle time.
-
3. Improve Demand Forecasting
Poor demand forecasting causes overproduction or shortages. Leverage historical data and AI-powered tools to predict seasonal trends and adjust accordingly.
-
4. Build Flexibility into Your Plan
Stay responsive to market changes with buffer capacity and flexible shift models. Modular production setups allow faster adaptation to demand fluctuations and new product requirements.
-
5. Improve Cross-Department Collaboration
A unified planning system helps sales, production, and procurement stay aligned. Transparent workflows ensure everyone is informed about current capacity and demand — making decisions easier and processes smoother.
Maximize Utilization, Minimize Losses: Future-Proof Your Production
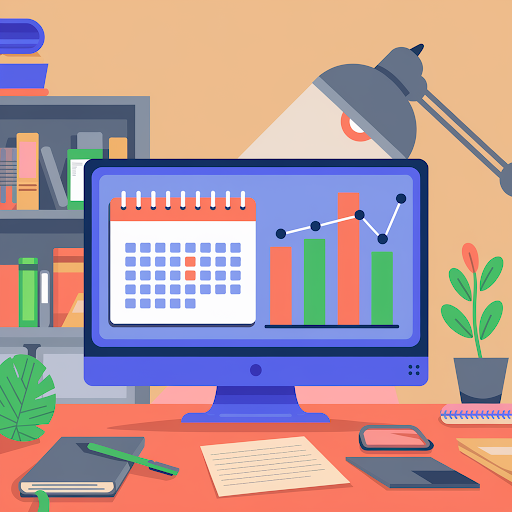
Future-ready production relies on optimized capacity planning.
With TEEP, digital planning tools, and proactive resource management, you can reduce downtime, boost machine utilization, and cut operational costs.
Now’s the perfect time to strengthen your capacity planning — for a more efficient, competitive, and resilient manufacturing operation.
👉 Discover how CapaPlanner can support your planning strategy.